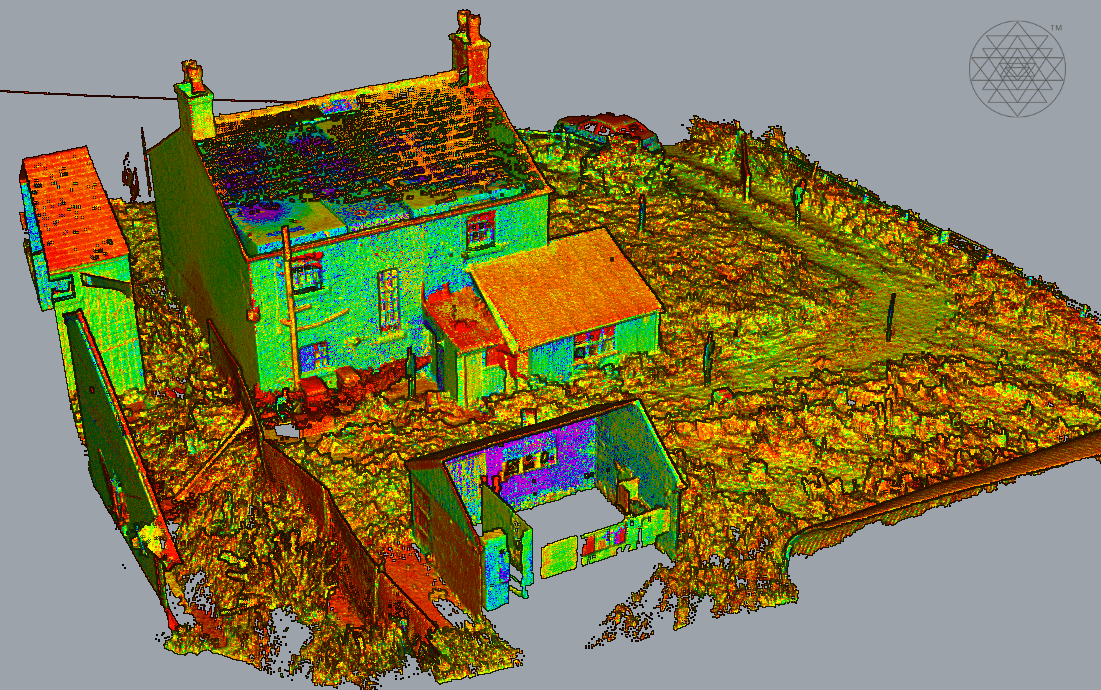
Table of Contents
Creating 3D models can be a challenging task, especially when starting from scratch. However, with the advancements in technology, 3D scanning and CAD software have made it possible to create stunning 3D models quickly and accurately. Our 3D scan to CAD solutions provides an efficient and reliable way to convert physical objects into digital models.
At the core of our 3D scan to CAD solutions is the 3D scanning technology that captures the geometry and texture of physical objects. We use high-quality 3D scanners that can capture objects with high precision and detail. These scanners use a variety of methods such as structured light, laser triangulation, and photogrammetry to capture the 3D data. The result is a point cloud that represents the surface geometry of the physical object.
Once the 3D data is captured, it is processed using advanced software algorithms that convert the point cloud into a CAD model. Our CAD software can recognize and extract features such as curves, surfaces, and edges from the point cloud. The software can also repair any defects and smooth the surfaces to ensure that the final model is accurate and of high quality.
How to Clean Up 3D Scanned Data for Accurate CAD Modeling
Cleaning up 3D scanned data is an important step in creating accurate CAD models. Here are some steps you can take to clean up your 3D scanned data for accurate CAD modeling:
Remove noise: 3D scanners can capture noise in the form of speckles, holes, and other anomalies. Use a noise reduction filter or a software tool that can remove noise from the scan.
Remove unwanted details: The 3D scanner can capture tiny details that are not needed in the CAD model. Use a tool to remove unwanted details that do not add value to the CAD model.
Repair holes and gaps: The 3D scanner can sometimes capture holes and gaps in the scan. Use a tool that can automatically repair these holes and gaps to ensure that the CAD model is accurate.
Smooth surfaces: The 3D scanner can sometimes capture rough surfaces that may not be needed in the CAD model. Use a tool to smooth surfaces to create a clean and accurate CAD model.
Align the data: 3D scanning can often result in misaligned data. Use a tool to align the data to ensure that the CAD model is accurate.
Check for accuracy: Once you have cleaned up the 3D scanned data, it is important to check for accuracy. Compare the cleaned-up data with the original scan to ensure that the CAD model is accurate.
By following these steps, you can create an accurate CAD model from 3D scanned data.
Exploring Different CAD Software Options for 3D Scan Data Processing
When it comes to processing 3D scan data, there are a number of CAD (Computer-Aided Design) software options available. The best option for you will depend on your specific needs, budget, and skill level.
Autodesk Meshmixer: Meshmixer is a free, easy-to-use 3D editing tool that allows you to edit and manipulate 3D scan data. It offers a wide range of tools for editing, smoothing, and repairing mesh files.
Blender: Blender is a free and open-source 3D creation software that can also be used for processing 3D scan data. It offers advanced features for modeling, sculpting, and animation.
Geomagic Design X: Geomagic Design X is a more advanced CAD software option specifically designed for processing 3D scan data. It offers powerful tools for reverse engineering, surface modeling, and quality inspection.
SolidWorks: SolidWorks is another popular CAD software option that offers advanced 3D modeling and design capabilities. It has a wide range of tools for processing 3D scan data, including mesh repair, surface modeling, and feature recognition.
MeshLab: MeshLab is a free, open-source software for processing and editing 3D scan data. It offers a range of tools for mesh processing, such as smoothing, decimation, and alignment.
Previous Blog: Expert BIM Coordination Services in Boston